Hemp Rebar
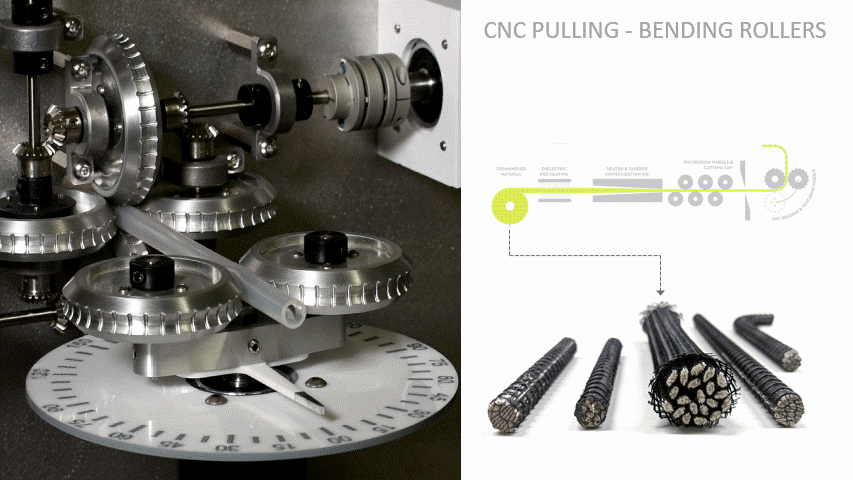
Rapid Pultrusion and Forming of Thermoplastic Composite Rebar
The American Society of Civil Engineers estimates that an additional 2.6 trillion dollars in funding over the next 10 years is necessary to adequately repair and maintain America's infrastructure. Infrastructure projects typically demand 75-100 years of service lives, a challenge with traditional reinforced concrete. Although non-corroding reinforcing bar (rebar), such as stainless steel and fiber-reinforced polymer (FRP), can achieve these service lives, they are costly. Additionally, FRP presents logistical challenges as it cannot be shaped in the field.
We introduce a natural fiber thermoplastic composite alternative for the concrete construction industry. The goal is to provide a technology that is more cost-effective, easier to install, and utilizes less embodied energy compared to current state of the art. The Natural Fiber-Reinforced Thermoplastic (NFRT) composite rebar designed for reinforced concrete seeks to match the mechanical and durability performance by weight of stainless steel or FRP but at a more economical price point. This is achieved by incorporating renewable and recycled materials and adopting streamlined logistics through on-site rebar fabrication and automated bending to designer specifications. Moreover, this rebar will demand less embodied energy during production, ultimately reducing the total environmental impact of reinforced concrete.
The feedstock for NFRT is a rope preform comprising unidirectional natural fiber yarns (e.g., hemp, flax) as reinforcement commingled with thermoplastic filaments as the matrix, tightly bound within a braided thermoplastic sleeve. Instead of the conventional pultruder setup with racks of reinforcement and polymer filament reels, our compact pultrusion machine processes the unconsolidated rope wound on a large reel. This simplifies the production of composite rebar, either in a micro-factory or at a construction job site. The selection of the combination of reinforcement and matrix at a specific fiber volume fraction (Vf) is based on acceptable interfacial shear strength between the materials and the rebar's tensile and bending modulus and/or strengths for particular infrastructure applications. The thermoplastic matrix may be homogeneous (e.g., PLA, PP) or a heterogeneous polymer blend, depending on mechanical properties, fiber/matrix bonding interfaces, and/or processing requirements.
Project Date: 2021 - Current
Researchers: Alexandros Tsamis, Daniel Martin Cohen, Daniel Walczyk, Sharmad Joshi.
Publications:
Joshi, Sharmad. Walczyk, Daniel. Wasti, Amogh. Borca-Tasciuc, Theodorian., Daniel Cohen,, Tsamis, Alexandros. 2023. Thermal Properties of Commingled Fibers for Pultrusion of Thermoplastic Biocomposites. Journal of Thermoplastic Composite Materials.
Cohen, Daniel. , Joshi, Sharmad. Walczyk, Daniel. Tsamis, Alexandros. 2022, Fibrewerks: An interscalar study into the viability of natural fibre composite rebar for cementitious materials. ACSA 2022 Intersections Research Conference: RESILIENT FUTURES
Cohen, Daniel. 2021. Hempwerks : non-corroding concrete reinforcing made with natural fiber and thermoplastics . MS thesis. Built Ecologies. School Of Architecture. (Rensselaer Polytechnic Institute, Troy, NY, 2021-08)